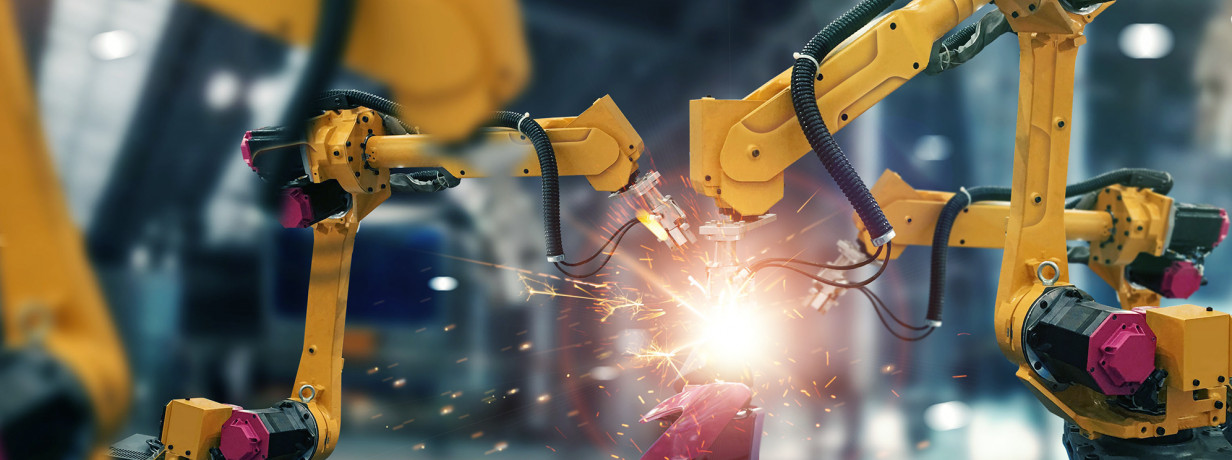
BALLUFF-Soluciones para el entorno de la soldadura
Aumento de la productividad en la soldadura automatizada
La gama de productos para soldadura es un grupo de productos Balluff de eficacia probada en la industria, diseñados para su uso en los entornos de soldadura automatizada más inhóspitos. Siguiendo las mejores prácticas a la hora de seleccionar los sensores y los componentes relacionados, las operaciones de soldadura de todos los sectores pueden reducir el tiempo de inactividad, el mantenimiento innecesario, los retrasos en la entrega y la pérdida de beneficios.
Balluff presenta un paquete completo de soluciones de soldadura que prolonga la vida útil de los sensores y aumenta la productividad en los entornos de soldadura más duros. Nos comprometemos a ayudar a los trabajadores de todos los niveles de la planta a identificar los problemas existentes, y ofrecemos soluciones que han sido probadas por nuestros clientes en los entornos de soldadura más duros durante décadas para proporcionar una mejora significativa del proceso y de la calidad de las piezas.
La expectativa estándar en la soldadura automatizada acepta menores costes de componentes combinados con un alto volumen de sustitución de componentes y de mantenimiento, reparación y operaciones (MRO). Los sensores dañados y los cables quemados provocan tiempos de inactividad no planificados y reducen la producción, lo que aumenta los costes salariales de las horas extraordinarias y crea un problema en los plazos de entrega. Nos asociamos con los clientes para desarrollar las mejores soluciones específicas para cada aplicación con el fin de aumentar la productividad en las áreas problemáticas:
- Dejar de desperdiciar sensores y destruir conectores
- Cambiar el paradigma del uso aceptado de los sensores de gran volumen
- Reducir el tiempo de inactividad debido a fallos en los sensores
- Reducir el consumo de sensores y conectores
- Aumentar la rentabilidad en toda la planta
La soldadura automatizada requiere soluciones robustas, ya que la mayoría de los componentes de automatización estándar y las prácticas de montaje básicas no suelen aguantar bien en las celdas de soldadura. Balluff ha trabajado durante décadas para lograr la excelencia operativa mediante el desarrollo de las mejores prácticas y soluciones para mejorar el tiempo de actividad y eliminar las molestas paradas por fallos en la automatización. Utilizamos nuestra pasión por la automatización y la tecnología duradera para la mejora continua para ayudar a alcanzar sus objetivos.
Problemas comunes en la soldadura automatizada y robótica
- Detección de tuercas y orientación de tuercas de soldadura
Una de las aplicaciones más comunes y frustrantes en la soldadura automatizada y robótica es la detección fiable de la presencia de una tuerca de soldadura. Existen algunas soluciones y tecnologías en el mercado que tienen distintos niveles de éxito. La detección de la tuerca de soldadura es muy específica de la aplicación: ¿Detectarla durante la carga o en una estación de comprobación secundaria? ¿De qué espacio se dispone para un sensor y un conector? ¿Se detecta por debajo de la pieza o por encima de ella? ¿Cuál es el tamaño o la forma de la tuerca? ¿Cuáles son las tolerancias? Cada tipo de tecnología aporta ventajas y puntos débiles en función de las respuestas a estas preguntas. - Daños por salpicaduras de soldadura y ruido en el campo de la soldadura
Los sensores de proximidad inductivos sin contacto deben realizar una amplia variedad de indicaciones de sujeción y anidamiento, así como funciones de poka-yoke en entornos de soldadura difíciles. La acumulación de salpicaduras de soldadura caliente, las elevadas temperaturas ambientales y los fuertes campos electromagnéticos emitidos por las pistolas de soldadura pueden provocar falsos disparos y degradar el rendimiento del sensor. - Daños físicos por impacto de carga
Los daños incidentales del sensor causados por impactos durante la carga de piezas pueden degradar significativamente el rendimiento del sensor, acortar su vida útil o incluso destruirlo. Los sensores de proximidad inductivos de cara de acero de Balluff pueden soportar múltiples impactos fuertes y abrasión, y a menudo tienen un largo alcance de detección para poder colocarlos fuera de peligro. - Quemado de cables y daños en la red
Las células de soldadura exigen las soluciones de conectividad más resistentes. Los restos de soldadura acortan la vida de un cable de diferentes maneras. Las salpicaduras de soldadura pueden acumularse en la cubierta, sacando el cable del conector. Las chispas de soldadura pueden quemar el cable provocando cortocircuitos en la conexión, y las temperaturas extremas del entorno pueden cocer los componentes. La familia de cables de alta durabilidad de Balluff se ha diseñado teniendo en cuenta los entornos de soldadura. Los cuerpos de los conectores son inmunes a las chispas de soldadura con tuercas recubiertas de PTFE para evitar que las salpicaduras se peguen o quemen los conectores. Esta familia tiene múltiples cubiertas de cable para soportar diferentes entornos.
Aplicaciones de la automatización de la soldadura
Selección del tamaño del sensor
Para los sensores de proximidad inductivos, el tamaño es importante. Cuanto más grande sea la cara de detección, mayor será el alcance del sensor. Esto tiene dos ramificaciones en una aplicación de soldadura automatizada. En primer lugar, puede ser difícil detectar el borde de una pieza con un sensor, por lo que se recomienda detectar la superficie, no el borde. Si un borde tiene que ser el objetivo, se recomienda que la cara del sensor tenga un diámetro similar al grosor de la pieza. En segundo lugar, es importante no utilizar mini sensores para detectar piezas grandes. Los mini sensores son más propensos a sufrir daños por las piezas grandes debido a su corto alcance de detección y a su pequeña masa. Estos mini sensores son potentes cuando se utilizan correctamente, pero deben usarse con moderación con piezas grandes, o guardarse para su uso en dispositivos de submontaje.
(1) Borde de la pieza (2) Sensor grande (3) Pieza grande (4) Sensor miniatura (5) Parte grande (6) Borde de la pieza (7) Sensor grande (8) Sensor miniatura
Desconexiones rápidas y cables de sacrificio
Los sensores con cable de salida son una de las opciones más baratas de la mayoría de los proveedores, pero no suelen ser adecuados para la automatización de la soldadura. El cable del sensor es uno de los puntos más comunes de fallo en una célula de soldadura debido a los daños causados por las salpicaduras de soldadura. Tener que sustituir un sensor electrónico que funciona perfectamente debido a un daño en el cable no es la excelencia operativa. Los sensores de desconexión rápida permiten sustituir sólo el componente que ha fallado y reducen el tiempo de sustitución. La inclusión de un cable de sacrificio corto en aplicaciones extremadamente duras puede reducir el tiempo de inactividad de la sustitución del cable cuando es inevitable debido al diseño de la aplicación.
(1) Sensor de salida de cable (2) Sensor de desconexión rápida (3) Cable de sacrificio
Siga comunicándose con las arquitecturas de E/S de soldadura
Los concentradores de E/S se han convertido en un dispositivo muy común para conectar los numerosos sensores utilizados en la soldadura automatizada. Estos dispositivos son buenos porque están conectados a una red y pueden proporcionar datos de diagnóstico, como cortocircuitos y sobrecargas. Sin embargo, muchos fabricantes tienen problemas con los cables de red dañados o los cables homerun que pueden causar problemas de comunicación intermitentes que son difíciles de solucionar. Al utilizar concentradores y maestros IO-Link para las E/S, el maestro puede montarse fuera de peligro para que siempre pueda comunicarse con el PLC y la red. Las E/S y los dispositivos de detección se montan en la célula de trabajo, donde pueden producirse los daños. Si un dispositivo falla, el maestro puede informar de los detalles a la cadena. Esta arquitectura permite mejorar la resolución de problemas gracias a la comunicación constante y a la disponibilidad de los diagnósticos.
(1) Entorno hostil (2) Colector de válvulas conectado a IO-Link (3) Bloque de E/S conectado a IO-Link
Solución rápida de problemas e intercambio en caliente
El tiempo es un recurso valioso. Cuando se produce un problema, los equipos de mantenimiento y los operarios necesitan encontrar rápidamente una solución y poner el equipo en funcionamiento. Al implementar E/S de montaje en máquina IP67, los puntos que fallan son más visibles y accesibles. Además, los diagnósticos proporcionados por los dispositivos inteligentes individuales pueden ayudar a reducir el alcance del problema y acelerar la recuperación. Los operarios pueden proporcionar a los técnicos detalles exactos del fallo y el técnico puede ahorrar tiempo al conocer y prepararse para el problema incluso antes de llegar al equipo.
(1) Posibles diagnósticos proporcionados: Dispositivo presente, dispositivo alimentado, funcionamiento marginal, lente sucia, objetivo más allá del rango de detección, cortocircuito detectado, sobrecarga detectada, bobina de salida abierta.
Seguimiento de contenedores de piezas y devolución de carros de estiba
Cuando se trasladan materiales entre las instalaciones de producción, es vital hacer un seguimiento de lo que ha salido del edificio y lo que se ha devuelto. Esto es aún más importante cuando se envían piezas a un cliente. Los carros de estiba y las estanterías especializadas para el traslado de piezas acabadas pueden tener un precio elevado. Si estas estanterías no se devuelven o se pierden, pueden mermar los márgenes de beneficio o dificultar la entrega de piezas de forma segura a un cliente. Al utilizar sistemas RFID UHF, los fabricantes registran cada carro que sale de las instalaciones, saben qué camión y a qué hora salió. Esto permite documentar la entrega y conocer la cadena de propiedad de los valiosos carros de estiba y estanterías.
(1) Procesador RFID BISV (2) Cabezal de lectura (3) Etiqueta RFID.