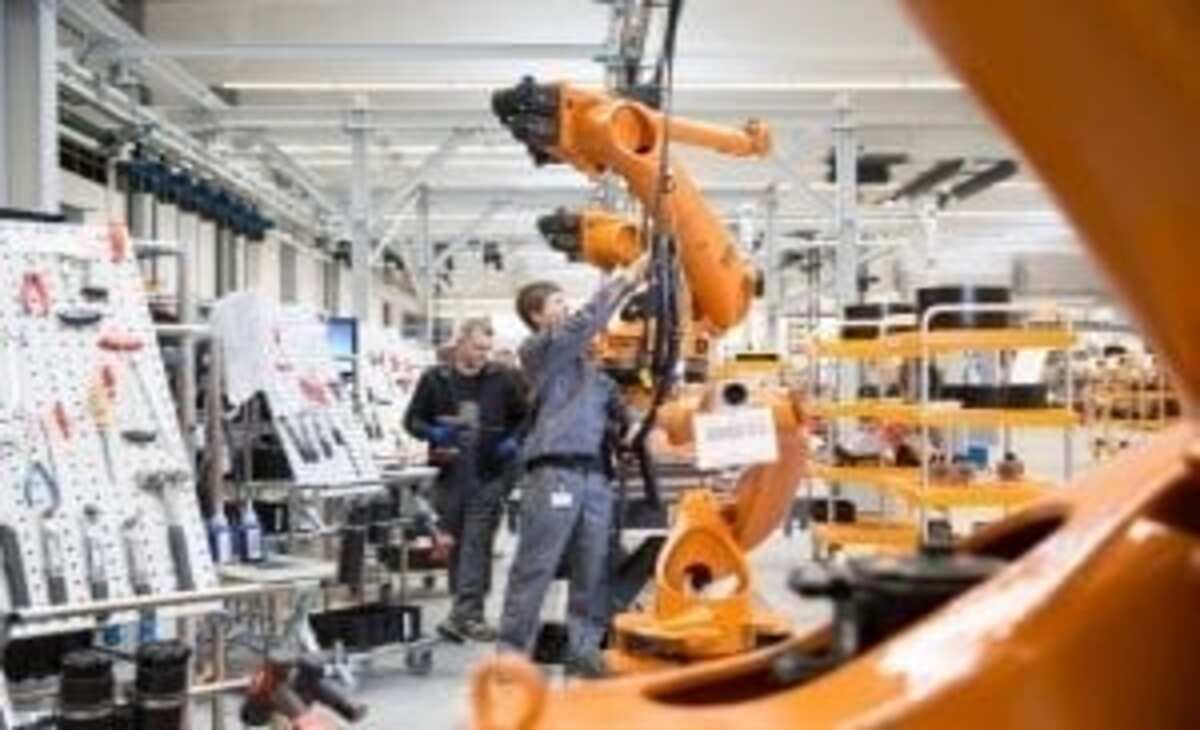
Es un robot: Cómo se hace un robot.
Los robots transportan cargas pesadas. Unen, sueldan y ensamblan piezas. Así es como se fabrican los smartphones, los coches y los aviones. Pero los robots, ¿quién los construye? Una persona que seguro que lo sabe es Sebastian Bodenmüller, director de KUKA Robot Assembly en Augsburgo.
“Cuando se trata de la producción de robots, muchos de nuestros visitantes piensan en escenas de Hollywood. Sin embargo, nuestra planta de montaje de robots no tiene nada que ver con las superproducciones de ciencia ficción”, responde Bodenmüller cuando se le pregunta por las expectativas con las que la mayoría de los visitantes entran en los talleres de producción. “Dicho esto, hemos integrado una amplia gama de aplicaciones avanzadas”, añade con un guiño. Entre las aplicaciones avanzadas a las que se refiere se encuentra, por ejemplo, la carretilla KMR, una plataforma de transporte autónoma que se asemeja a una carretilla elevadora y que se utiliza en las instalaciones de producción. Pero más adelante hablaremos de esto.
Los robots se construyen en una línea de producción.
En Augsburgo, KUKA produce tanto modelos de serie como pequeños robots. El tiempo de ciclo es de algo menos de 15 minutos. Es decir, cada hora salen de la línea de producción unos cuatro robots terminados. Los modelos de serie, que representan entre el 60 y el 70 por ciento de nuestra producción, se fabrican en una línea de montaje, mientras que el 30-40 por ciento restante, entre los que se encuentran el LBR iiwa, el KR Agilus y el KR Titan, se producen en líneas separadas o en estaciones de montaje individuales. Esto se debe, por ejemplo, al peso del KR Titan o a los complejos requisitos mecatrónicos del LBR iiwa.
Todo comienza con el sistema mecánico.
El primer paso del montaje de todos los robots fabricados en la línea es el montaje del eje 1, que comprende el bastidor base, el reductor y la llamada columna giratoria. Para ello se dispone de una célula robótica flexible. Aquí, los trabajadores pueden realizar el atornillado y otras tareas complejas, mientras un robot KR 1000 Titan mueve las piezas individuales, algunas de las cuales son muy pesadas.
Además, un KR Agilus aplica el compuesto de sellado al engranaje. A continuación, el personal de producción ensambla gradualmente los ejes 2 a 6. Juntos, los ejes 4, 5 y 6 constituyen la compleja muñeca en línea en la que se instalan la mitad de los numerosos componentes individuales.
La automatización y la Industria 4.0 se ponen en práctica en Augsburgo.
Como la mayoría de los elementos principales del robot, las piezas de la muñeca en línea se fabrican en el taller de mecanizado de Augsburgo. La particularidad es que un robot KUKA de la serie QUANTEC carga las piezas sin mecanizar en el centro de mecanizado en el que se fabrican los elementos. Entre los ciclos de carga, el robot mecaniza y desbarba adicionalmente los componentes. De este modo, todos los pasos de mecanizado necesarios para la fabricación de la pieza pueden llevarse a cabo en una sola célula.
Los tornillos necesarios para el montaje de las piezas acabadas encuentran su camino en el lugar correcto con la ayuda de un KMR iiwa. La plataforma omnidireccional, en la que está montado un LBR iiwa, no sólo reconoce qué tornillo va a dónde, con la ayuda de un escáner RFID, sino que al mismo tiempo sabe qué mercancías salen del almacén cuando y ordena automáticamente su reposición. También lleva las piezas a donde se necesitan. De este modo, el personal se libera de las tediosas tareas de clasificación.
Es hora de dar un toque de color.
Desde el punto de vista mecánico, el robot está terminado. Ahora es el momento de la pintura. Para ello se dispone de dos cabinas. De forma estándar, los robots se pintan de color naranja KUKA. Sin embargo, si el cliente lo solicita, se pueden realizar todos los colores y diseños imaginables, o incluso la pintura flip-flop, que cambia de color según el ángulo desde el que se mire. Esto también se aplica a los acabados de pintura especiales, como la pintura para fundición, que es resistente al calor y a los ácidos, o la pintura para salas limpias para aplicaciones estériles.
Independientemente de la pintura utilizada para el robot, éste debe pasar por la cabina de secado. Sólo entonces la pintura a base de agua, y por tanto especialmente respetuosa con el medio ambiente, puede secarse rápidamente.
Montaje eléctrico: los soportes de tensión.
La tensión aumenta cuando el robot pasa del taller de pintura al montaje eléctrico. Aquí los empleados trabajan en el sistema de suministro de energía y en el control de los motores. Al final del ciclo, una vez comprobada la tensión de interferencia y el correcto cableado del robot, una carretilla elevadora KMR totalmente automatizada lleva el robot montado desde el montaje eléctrico hasta la aceptación del producto.
Comprobación exhaustiva en la aceptación del robot.
En la aceptación del producto, el robot se pone a prueba. Se pone en funcionamiento durante una media de 45 minutos para que el aceite alcance la temperatura y la viscosidad adecuadas. De este modo, se detectan enseguida las posibles fugas. Además, aquí se cargan los datos de la máquina en el robot y se montan las herramientas de medición importantes en la brida para poder calibrar el robot. Sólo cuando todos los detalles técnicos y los requisitos son cien por cien satisfactorios, el robot puede pasar a la inspección de acabado.
Salir al gran mundo.
En el último paso, la inspección de acabado, el robot se somete de nuevo a una exhaustiva comprobación visual. A continuación, se colocan los carteles de advertencia e instrucciones para el funcionamiento del robot y la placa de identificación. A continuación, el robot se embala y se envía.
Durante la visita a la planta de producción de robots de KUKA en Augsburgo, una cosa quedó clara: no tiene nada que ver con Hollywood. Sin embargo, los robots que trabajan de forma autónoma en los talleres de producción son muy interesantes.